|
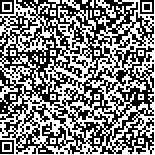 二维码(扫一下试试看!) |
Analysis of Corrosion Causes of Heating Surface of Alkali Recovery Furnace |
Received:February 19, 2020 |
DOI:10.11980/j.issn.0254-508X.2020.05.007 |
Key Words:alkali recovery furnace black liquor SEM analysis XRD analysis causes of corrosion |
Fund Project:生物质锅炉受热面腐蚀机理实验研究及寿命预测(CX2018SS13)。 |
Author Name | Affiliation | Postcode | SHU Yongxian | School of Energy and Power Engineering, Changsha University of Science and Technology, Changsha, Hu’nan Province, 410114 | 410114 | YAN Xiaozhong | School of Energy and Power Engineering, Changsha University of Science and Technology, Changsha, Hu’nan Province, 410114 | 410114 | OUYANG Guobin | School of Energy and Power Engineering, Changsha University of Science and Technology, Changsha, Hu’nan Province, 410114 | 410114 | WANG Chao | Juntai New Material Technology Co., Ltd., Huaihua, Hu’nan Province, 418005 | 418005 | ZHAO Lixin | Juntai New Material Technology Co., Ltd., Huaihua, Hu’nan Province, 418005 | 418005 |
|
Hits: 4711 |
Download times: 3503 |
Abstract:In order to study the cause of serious corrosion of alkali recovery furnace in the operation, a 2200 tds/d alkali recovery furnace was taken as the research object. The causes of the corrosion of the heating surface of the alkali recovery furnace were studied by analyzing the characteristics of the black liquor, measuring the thickness changes of the heating surface, SEM analysis of the water wall cutting pipe and XRD analysis of the corrosion products. The results showed that during black liquor combustion the corrosion of the alkali recovery furnace mainly occurred in the high temperature load area and part of low temperature heating surface at the burners line places of each burners and water wall of the middle and lower layers. The corrosion in the furnace was continuously diffused and intensified, which was mainly caused by the action of corrosive gas produced by black liquor combustion, diffusible corrosion products with high temperature corrosiveness, high temperature oxidation-reduction and sulfuration. The uneven velocity field of the tail gas led to the corrosion of the low temperature heating surface. The higher design flow rate of the flue gas of the first stage superheater at the upper part of the furnace heating surface suffered from alternately corrosion and wear. Based on the finding of the research, the reasonable anticorrosion measures were put forward. |
View Full Text HTML View/Add Comment Download reader |
|
|
|