摘要
为提升涂布机烘箱的干燥特性,本研究针对风嘴结构及其附近区域展开研究,分析风嘴多结构参数对内部流场特性的交互影响。借助有限元分析和响应面法,建立烘箱风嘴多结构参数交互影响下的流场特性数学回归模型,基于此进行风嘴结构的优化设计,并将优化结果与仿真值进行误差比较,验证所构建回归模型的准确性。结果表明,构建的含有多结构参数的风嘴流场特性回归模型拟合度较好,基材温度、基材表面风速、基材压力3组响应值的预测值和仿真实验值误差均小于3%,能够较好描述风嘴局部流场特性变化规律。
涂布产品一般由多层材料复合而成,对材料进行涂布可以完善材料的理化特
烘箱的干燥性能主要由其箱体的结构及风嘴的结构和分布状态决定,国内外学者针对烘箱和风嘴结构等展开了广泛研究。针对烘箱结构,张海燕
风嘴是烘箱结构的核心部件,有调整热风分布、组织热风流向的作用,其结构参数对内部流场影响不可忽视。Jeong
由于烘箱风嘴结构包含多个结构变量参数,各变量参数对流场特性的交互影响不可忽视,因此,本研究借助有限元分析和响应面方法,在有限元仿真得到流场特性的基础上,应用响应面分析方法建立烘箱风嘴多结构参数交互影响下流场特性的数学回归模型,验证模型准确性后,进行风嘴结构的优化设计,并对优化结果进行仿真验证,从而为风嘴结构设计提供一定的参考。
涂布式烘箱风嘴结构见
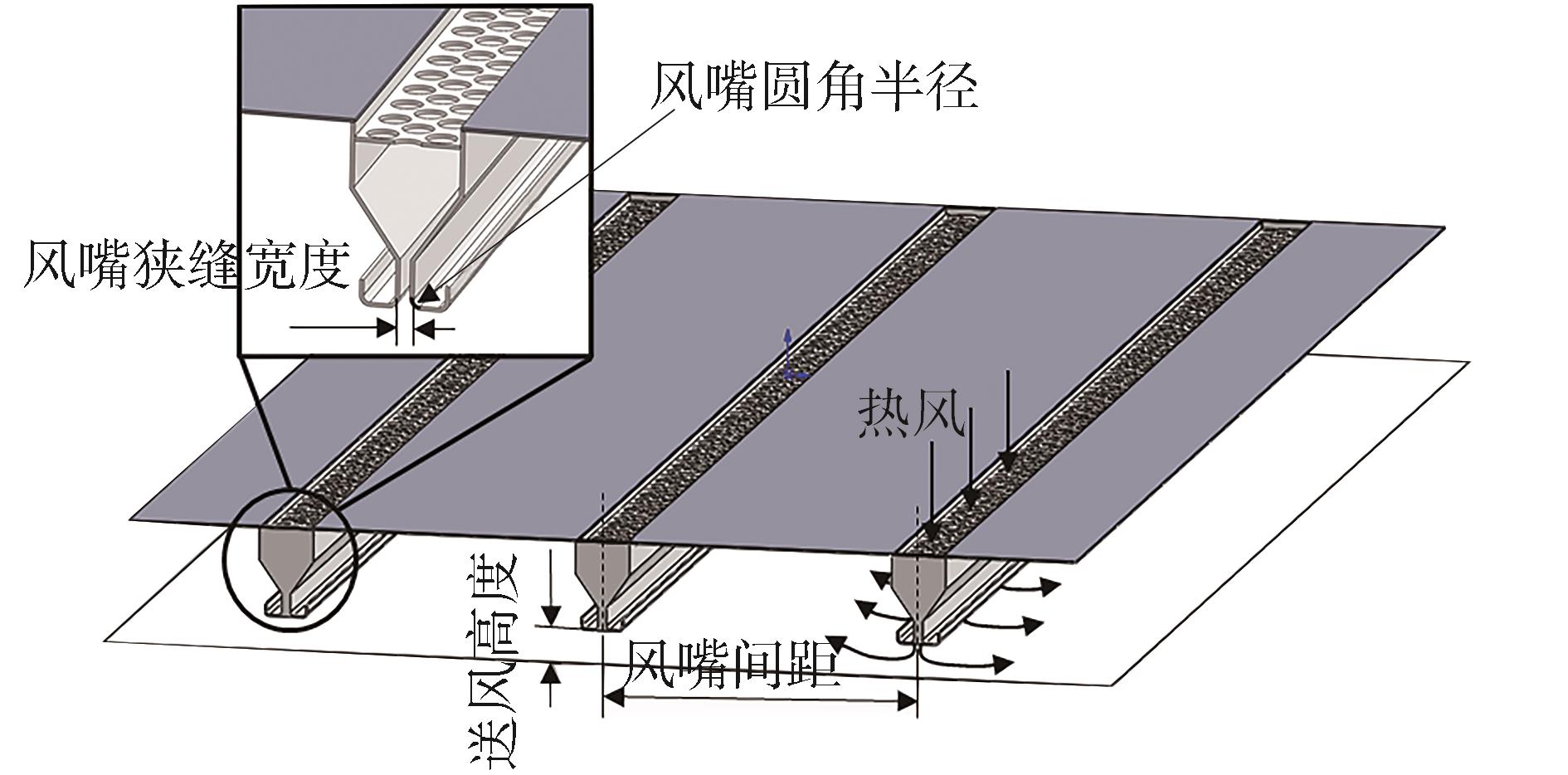
图1 风嘴几何模型及主要结构参数
Fig. 1 Geometric model and main structural parameters of the nozzle
由
参数 | 尺寸 |
---|---|
风嘴狭缝宽度 | 4 |
风嘴圆角半径 | 4 |
送风高度 | 30 |
风嘴间距 | 250 |
对建立的风嘴几何模型进行布尔运算得到流体域模型,然后对其进行网格划分,对其中具有较大速度变化的热风入口处、匀风板处、风嘴出口处进行局部加密,并在基材表面设置边界层网格以提高关键区域计算精度,对网格划分结果进行检查,扭曲度和歪斜度等网格质量均满足仿真要求,未出现负体积网格,网格模型如
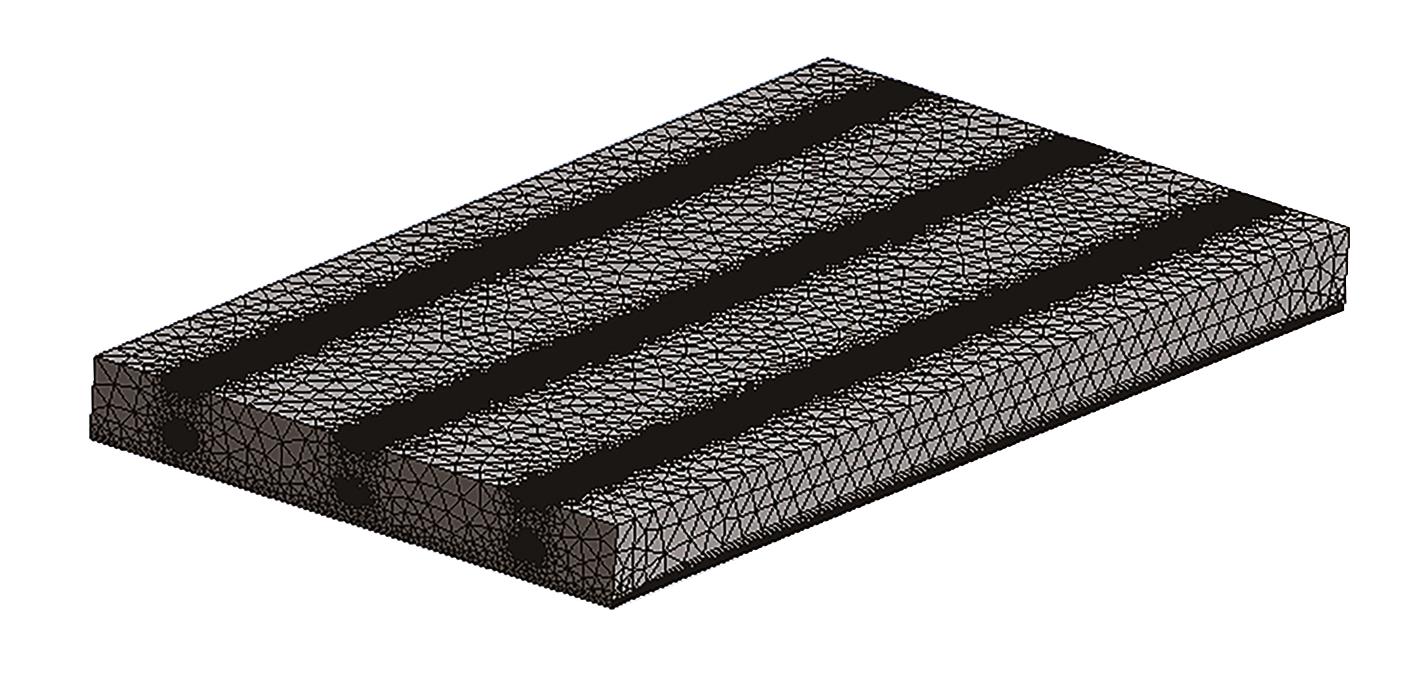
图2 风嘴网格模型
Fig. 2 Grid model of nozzle
本研究设置风嘴模型边界条件为速度入口,入口热风速度4 m/s,从入口垂直吹入,热风温度90 ℃,默认出口选择压力出口,基材处设置移动换热壁面,移动速度60 m/min,其余未标注边界均为固定换热壁面,风嘴几何模型具体边界条件设置见
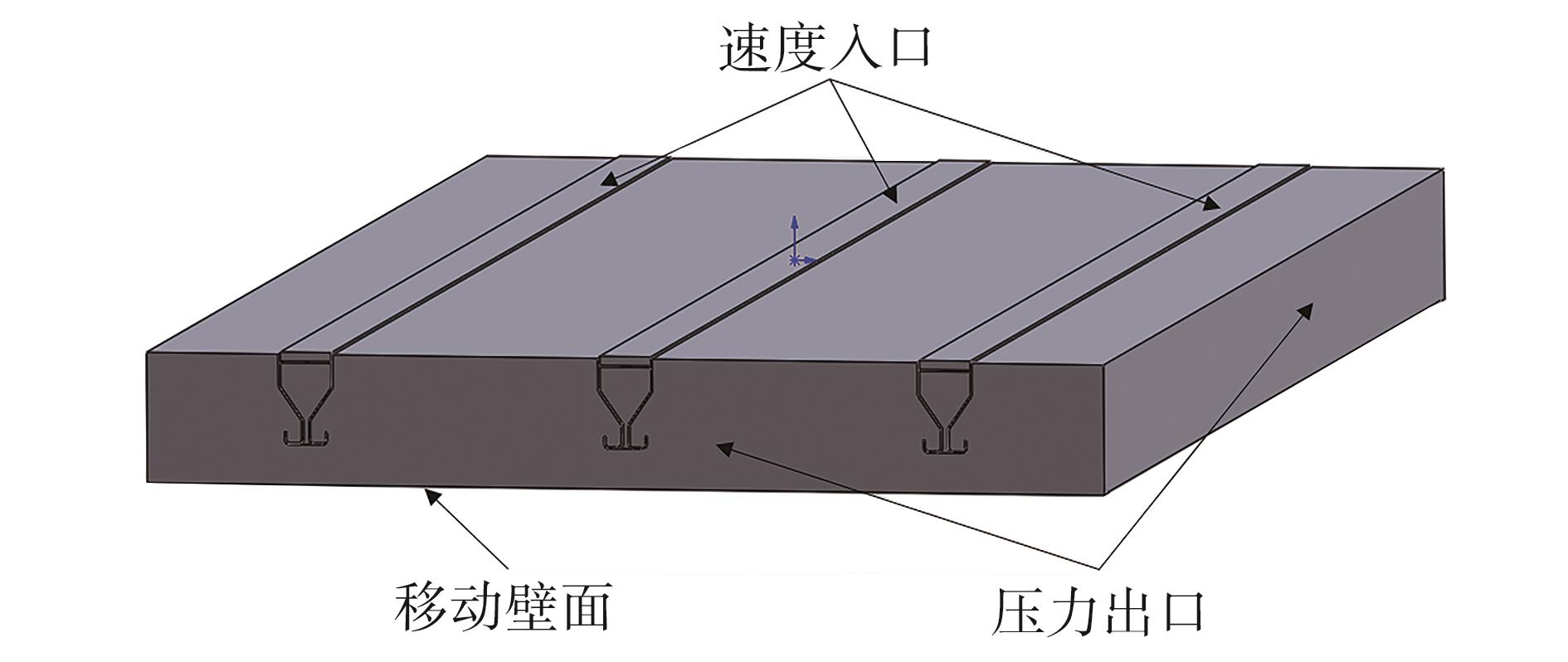
图3 风嘴几何模型边界条件示意图
Fig. 3 Boundary condition diagram of nozzle geomertic model
仿真模型计算完成后,对基材进行后处理提取云图,分析基材温度和基材压力云图(
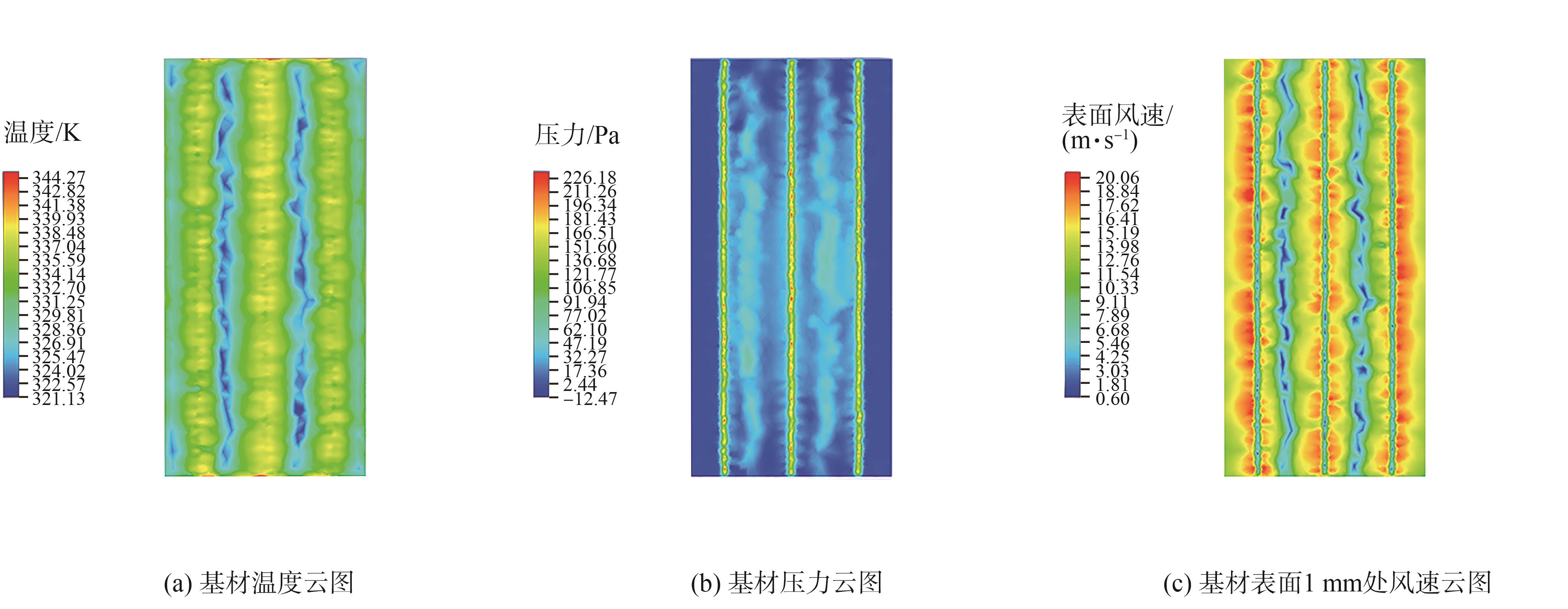
图4 基材流场云图
Fig. 4 Flow field cloud diagram of substrate
基材流场云图可定性展示风嘴内部温度、压力、表面风速的分布状态,为分析风嘴内部流场特性提供了客观依据。为准确评估热风场性能,需结合对应位置处数据进行定量分析。本研究的数据选择基材温度、压力、表面1 mm处风速,各组参数分别设置点云并提取500个数据,计算求得平均值,进行后续分析。
响应面法(response surface methodology, RSM)是一种有效的统计方法,利用合理的实验设计及所得数据,可以建立响应因素和输出响应值之间的回归模型,并对系统中的响应值进行优化从而得到优化后的自变量参数组合,经常被用于工程和科学研究之中,适当设计方法的选取,可大大减少实验次数,从而提高实验效
本研究选择风嘴狭缝宽度、风嘴圆角半径、送风高度、风嘴间距为响应因素,为方便回归模型拟合同时提高数据处理效率,将以上响应因素分别用X1、X2、X3、X4表示,每个参数设置3水平(即3组数据),因素水平编码表如
水平 | X1/mm | X2/mm | X3/mm | X4/mm |
---|---|---|---|---|
-1 | 3 | 3 | 20 | 200 |
0 | 4 | 4 | 25 | 225 |
1 | 5 | 5 | 30 | 250 |
选择基材温度(Y1)、基材表面风速(Y2)、基材压力(Y3)作为响应值,依据
实验编号 | X1/mm | X2/mm | X3/mm | X4/mm | Y1/K | Y2/(m· | Y3/Pa |
---|---|---|---|---|---|---|---|
1 | -1 | -1 | 0 | 0 | 331.67 | 14.58 | 41.35 |
2 | 1 | -1 | 0 | 0 | 332.96 | 13.51 | 31.93 |
3 | -1 | 1 | 0 | 0 | 331.20 | 11.74 | 26.24 |
4 | 1 | 1 | 0 | 0 | 331.48 | 11.13 | 25.24 |
5 | 0 | 0 | -1 | -1 | 333.82 | 13.47 | 36.99 |
6 | 0 | 0 | 1 | -1 | 331.61 | 11.94 | 33.54 |
7 | 0 | 0 | -1 | 1 | 332.25 | 13.24 | 26.83 |
8 | 0 | 0 | 1 | 1 | 330.24 | 11.80 | 26.24 |
9 | -1 | 0 | 0 | -1 | 332.68 | 13.73 | 37.69 |
10 | 1 | 0 | 0 | -1 | 332.82 | 11.99 | 34.52 |
11 | -1 | 0 | 0 | 1 | 330.90 | 13.29 | 30.78 |
12 | 1 | 0 | 0 | 1 | 332.13 | 11.70 | 24.25 |
13 | 0 | -1 | -1 | 0 | 333.53 | 14.67 | 38.59 |
14 | 0 | 1 | -1 | 0 | 332.71 | 12.37 | 26.45 |
15 | 0 | -1 | 1 | 0 | 331.66 | 13.40 | 32.39 |
16 | 0 | 1 | 1 | 0 | 330.35 | 10.54 | 26.97 |
17 | -1 | 0 | -1 | 0 | 333.10 | 14.15 | 33.89 |
18 | 1 | 0 | -1 | 0 | 333.47 | 13.19 | 29.31 |
19 | -1 | 0 | 1 | 0 | 330.46 | 12.60 | 32.52 |
20 | 1 | 0 | 1 | 0 | 331.35 | 11.30 | 25.77 |
21 | 0 | -1 | 0 | -1 | 333.20 | 14.29 | 41.18 |
22 | 0 | 1 | 0 | -1 | 331.91 | 11.37 | 31.29 |
23 | 0 | -1 | 0 | 1 | 332.18 | 14.02 | 30.33 |
24 | 0 | 1 | 0 | 1 | 330.94 | 11.21 | 22.08 |
25 | 0 | 0 | 0 | 0 | 331.82 | 12.73 | 31.18 |
26 | 0 | 0 | 0 | 0 | 331.73 | 12.69 | 31.15 |
27 | 0 | 0 | 0 | 0 | 331.92 | 12.21 | 30.56 |
28 | 0 | 0 | 0 | 0 | 331.57 | 12.54 | 31.14 |
29 | 0 | 0 | 0 | 0 | 331.72 | 12.51 | 30.54 |
借助Design Expert 10软件对
基材温度方差分析如
来源 | 平方和 | 自由度 | 均方 | F值 | P值 |
---|---|---|---|---|---|
模型 | 25.28 | 14 | 1.81 | 54.35 | <0.000 1 |
X1 | 1.47 | 1 | 1.47 | 44.25 | <0.000 1 |
X2 | 3.64 | 1 | 3.64 | 109.60 | <0.000 1 |
X3 | 14.54 | 1 | 14.54 | 437.74 | <0.000 1 |
X4 | 4.56 | 1 | 4.56 | 137.36 | <0.000 1 |
X1X2 | 0.26 | 1 | 0.26 | 7.68 | 0.015 0 |
X1X3 | 0.07 | 1 | 0.07 | 2.03 | 0.175 6 |
X1X4 | 0.30 | 1 | 0.30 | 8.94 | 0.009 7 |
X2X3 | 0.06 | 1 | 0.06 | 1.81 | 0.200 3 |
X2X4 | 0 | 1 | 0 | 0.02 | 0.892 9 |
X3X4 | 0.01 | 1 | 0.01 | 0.30 | 0.591 9 |
X | 0.10 | 1 | 0.10 | 3.08 | 0.100 9 |
X | 0.03 | 1 | 0.03 | 1.01 | 0.332 0 |
X | 0.18 | 1 | 0.18 | 5.44 | 0.035 1 |
X | 0.22 | 1 | 0.22 | 6.55 | 0.022 7 |
残差 | 0.47 | 14 | 0.03 | ||
失拟项 | 0.40 | 10 | 0.04 | 2.36 | 0.212 0 |
纯误差 | 0.07 | 4 | 0.02 | ||
其他 |
AP=27.87,C.V=0.06% |
注 P<0.01为差异极显著;P<0.05为差异显著;P>0.05为差异不显著,以下同。
建立基材温度(Y1)关于风嘴狭缝宽度(X1)、风嘴圆角半径(X2)、送风高度(X3)、风嘴间距(X4)4个因素的回归模型,如
| (1) |
结合
基材表面风速方差分析如
来源 | 平方和 | 自由度 | 均方 | F值 | P值 |
---|---|---|---|---|---|
模型 | 34.13 | 14 | 2.44 | 52.61 | <0.000 1 |
X1 | 4.40 | 1 | 4.40 | 95.06 | <0.000 1 |
X2 | 21.63 | 1 | 21.63 | 466.78 | <0.000 1 |
X3 | 7.54 | 1 | 7.54 | 162.66 | <0.000 1 |
X4 | 0.20 | 1 | 0.20 | 4.21 | 0.059 4 |
X1X2 | 0.05 | 1 | 0.05 | 1.14 | 0.303 4 |
X1X3 | 0.03 | 1 | 0.03 | 0.62 | 0.442 8 |
X1X4 | 0.01 | 1 | 0.01 | 0.12 | 0.732 7 |
X2X3 | 0.08 | 1 | 0.08 | 1.69 | 0.214 3 |
X2X4 | 0 | 1 | 0 | 0.07 | 0.802 0 |
X3X4 | 0 | 1 | 0 | 0.04 | 0.837 4 |
X | 0.11 | 1 | 0.11 | 2.29 | 0.152 6 |
X | 0.09 | 1 | 0.09 | 1.94 | 0.185 0 |
X | 0.06 | 1 | 0.06 | 1.34 | 0.266 4 |
X | 0 | 1 | 0.00 | 0.06 | 0.813 4 |
残差 | 0.65 | 14 | 0.05 | ||
失拟项 | 0.48 | 10 | 0.05 | 1.14 | 0.488 4 |
纯误差 | 0.17 | 4 | 0.04 | ||
其他 |
AP=28.22,C.V=1.70% |
建立基材表面风速(Y2)关于风嘴狭缝宽度(X1)、风嘴圆角半径(X2)、送风高度(X3)、风嘴间距(X4)4个因素的回归模型,如
(2) |
结合
基材压力方差分析如
来源 | 平方和 | 自由度 | 均方 | F值 | P值 | |
---|---|---|---|---|---|---|
模型 | 663.61 | 14 | 47.40 | 97.78 | <0.000 1 | |
X1 | 82.43 | 1 | 82.43 | 170.02 | <0.000 1 | |
X2 | 275.52 | 1 | 275.52 | 568.34 | <0.000 1 | |
X3 | 17.84 | 1 | 17.84 | 36.79 | <0.000 1 | |
X4 | 249.34 | 1 | 249.34 | 514.33 | <0.000 1 | |
X1X2 | 17.72 | 1 | 17.72 | 36.56 | <0.000 1 | |
X1X3 | 1.18 | 1 | 1.18 | 2.43 | 0.141 5 | |
X1X4 | 2.82 | 1 | 2.82 | 5.82 | 0.030 1 | |
X2X3 | 11.29 | 1 | 11.29 | 23.29 | 0.000 3 | |
X2X4 | 0.67 | 1 | 0.67 | 1.39 | 0.258 5 | |
X3X4 | 2.04 | 1 | 2.04 | 4.22 | 0.059 2 | |
X | 0.11 | 1 | 0.11 | 0.23 | 0.640 5 | |
X | 0.26 | 1 | 0.26 | 0.53 | 0.478 1 | |
X | 0.89 | 1 | 0.89 | 1.83 | 0.197 9 | |
X | 1.09 | 1 | 1.09 | 2.24 | 0.156 6 | |
残差 | 6.79 | 14 | 0.48 | |||
失拟项 | 6.34 | 10 | 0.63 | 5.73 | 0.053 5 | |
纯误差 | 0.44 | 4 | 0.11 | |||
其他 |
AP=37.34,C.V=2.24% |
建立基材压力(Y3)关于风嘴狭缝宽度(X1)、风嘴圆角半径(X2)、送风高度(X3)、风嘴间距(X4)4个因素的回归模型,如
(3) |
结合
响应面图是各影响因素两两交互作用形成的三维曲面图,研究其他因素不变时,剩余2个因素交互作用对响应值的影响程度,响应曲面图变化幅度越大,说明对应自变量对响应值的影响越大,反之则越小。
两因素交互作用对基材温度的三维响应面图如
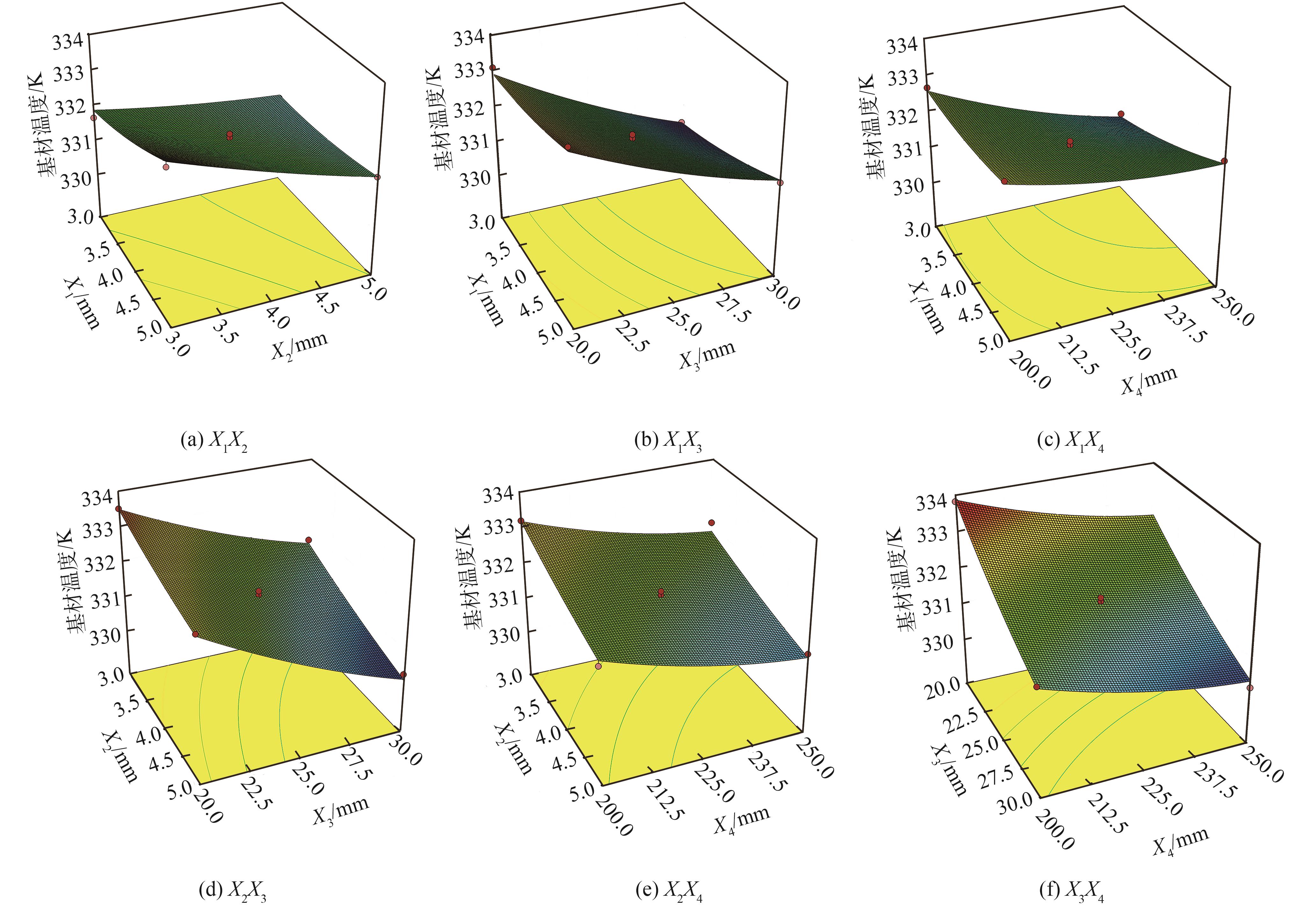
图5 基材温度的三维响应面图
Fig. 5 Three-dimensional response surface diagram of substrate temperature
如
对
图序 | 响应因素/mm | 响应值Y1/K | 增幅/% | |||
---|---|---|---|---|---|---|
定量 | 变化量 | 初值 | 末值 | |||
5(a) | X2=3 | X1初=3 | X1末=5 | 331.67 | 332.96 | 0.39 |
X1=5 | X2初=5 | X2末=3 | 331.48 | 332.96 | 0.45 | |
5(c) | X4=200 | X1初=3 | X1末=5 | 332.68 | 332.82 | 0.04 |
X1=5 | X4初=250 | X4末=200 | 332.13 | 332.82 | 0.21 |
由
两因素交互作用对基材表面风速的三维响应面图如
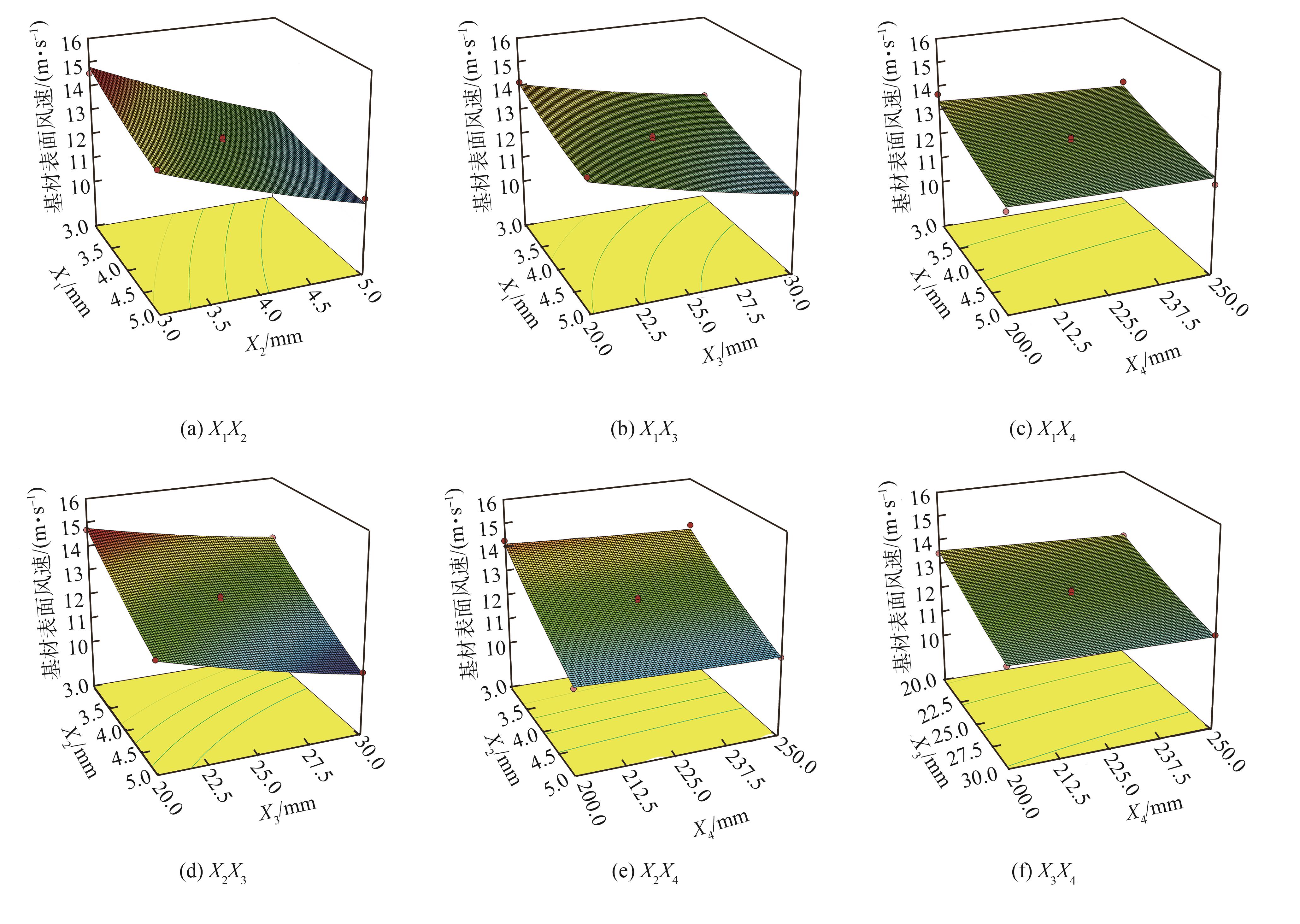
图6 基材表面风速三维响应面图
Fig. 6 Three-dimensional response surface diagram of substrate surface wind speed
分析
两因素交互作用对基材压力的三维响应面图如
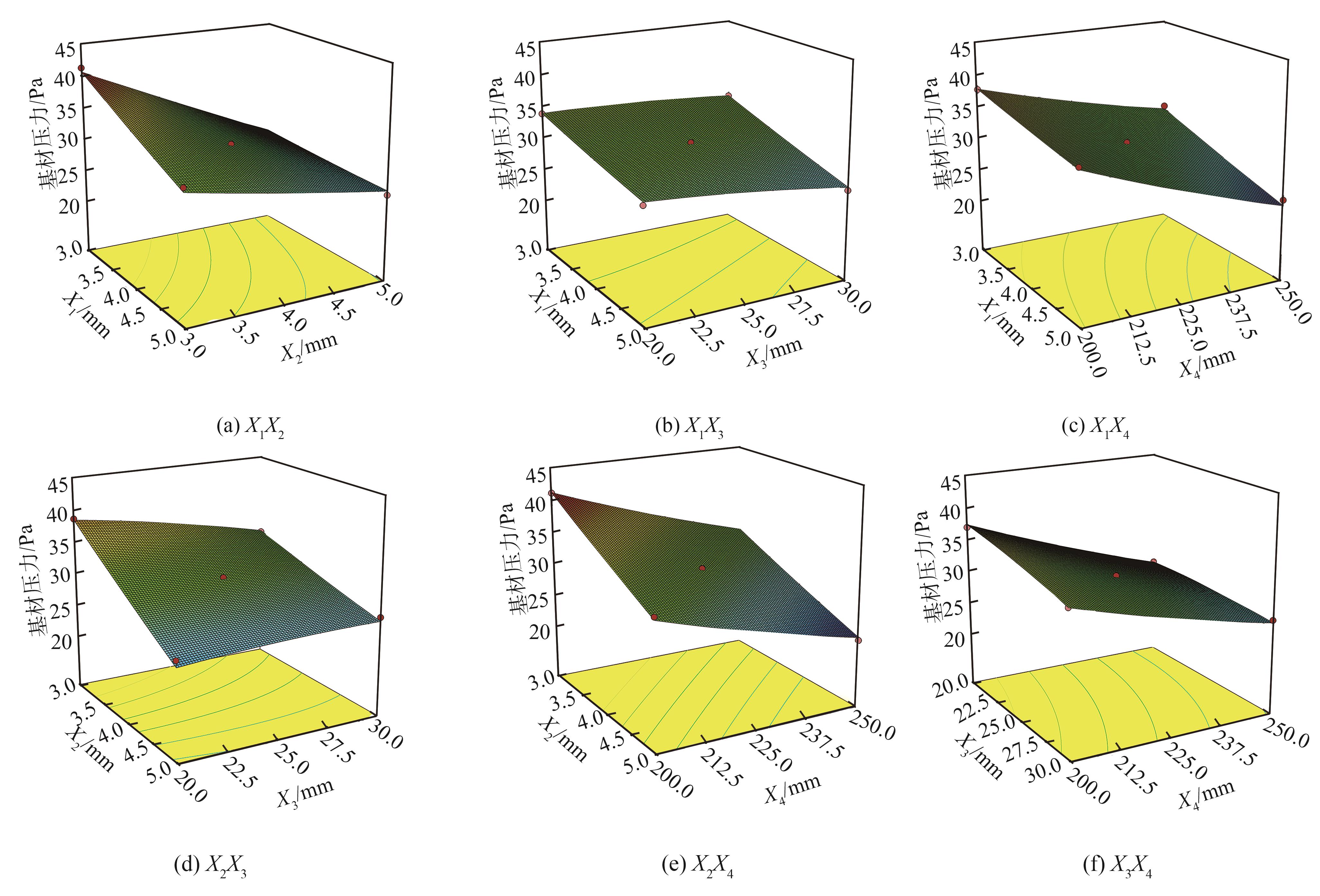
图7 基材压力三维响应面图
Fig. 7 Three-dimensional response surface diagram of substrate pressure
如
对
图序 | 响应因素/mm | 响应值Y3/Pa | 增幅/% | |||
---|---|---|---|---|---|---|
定量 | 变化量 | 初值 | 末值 | |||
7(a) | X2=3 | X1初=5 | X1末=3 | 31.93 | 41.35 | 29.5 |
X1=3 | X2初=5 | X2末=3 | 26.24 | 41.35 | 57.6 | |
7(c) | X4=200 | X1初=5 | X1末=3 | 34.52 | 37.69 | 9.18 |
X1=3 | X4初=250 | X4末=200 | 30.78 | 37.69 | 22.5 | |
7(d) | X3=20 | X2初=5 | X2末=3 | 26.45 | 38.59 | 45.9 |
X2=3 | X3初=30 | X3末=20 | 32.39 | 38.59 | 19.1 |
由
基于2.2建立的基材温度、基材表面风速、基材压力回归模型对风嘴流场特性进行优化,针对各响应值优化目标,设定基材温度取最大值,基材表面风速和基材压力取实验所得范围值,获得风嘴结构优化条件和对应的响应值(
组号 | 风嘴狭缝宽度/mm | 风嘴圆角半径/mm | 送风高度/mm | 风嘴间距/mm | 基材温度/K | 基材表面风速/(m· | 基材压力/Pa |
---|---|---|---|---|---|---|---|
仿真值 | 4.0 | 4.0 | 20.0 | 200.0 | 333.815 | 13.472 | 36.986 |
预测值 | 3.941 | 3.959 | 20.213 | 200.008 | 333.824 | 13.639 | 37.754 |
相对误差值 | 0.03% | 1.24% | 2.08% |
本研究借助有限元分析和响应面法,研究了涂布机烘箱风嘴结构多参数交互作用对流场特性的影响,并对流场进行优化得到了最佳的风嘴结构。
4.1 采用响应面法研究了风嘴结构多参数交互作用对其流场特性的影响,弥补了现有研究中仅为风嘴结构单因素分析问题存在的不足。
4.2 构建了风嘴结构多参数影响下的流场特性回归模型,经对模型决定系数、显著性等指标判定,模型具有较好的拟合度,能够对风嘴区域流场进行可靠分析和预测。
4.3 基于建立的回归模型对风嘴流场进行优化得到新的风嘴结构参数,经与仿真结果对比,3组响应值所得误差均<3%,验证了回归模型的准确性。
参 考 文 献
李路海,方一. 涂布复合技术概论[M]. 北京: 文化发展出版社, 2017:1-10. [百度学术]
LI L H,FANG Y. Introduction of coating composite technology[M].Beijing:Cultural Development Press,2017:1-10. [百度学术]
JEONG T G, SEO Y H, KIM S, et al. Roll to roll air-floating oven drying process design and analysis for printed electronics[J].International Journal of Precision Engineering and Manufacturing, 2014, 15:1303-1310. [百度学术]
孟友彬,廖界丰.悬浮干燥在涂布机干燥系统中的应用研究[J].中国高新科技,2022(12):153-155. [百度学术]
MENG Y B, LIAO J F. Research on application of suspension drying in coater drying system[J]. China High and New Technology,2022(12):153-155. [百度学术]
张海燕,刘金金,薛志成,等.涂布机悬浮烘箱的结构参数优化[J].机械设计与研究,2015,31(4):142-146. [百度学术]
ZHANG H Y, LIU J J, XUE Z C, et al. A Rescerch on structural parameter optimization of suspended drying equipment in coating machine[J].Machine Design and Research, 2015, 31(4):142-146. [百度学术]
LIU P, LEI X, XU Z, et al. Study on the structure optimization of oven duct system in gravure press[C]//Proceedings of 2019 10th China Academic Conference on Printing and Packaging. Singapore: Springer, 2020: 464-473. [百度学术]
袁启龙,李春霞,许力,等.基于Fluent的干法造纸负压箱流场特性分析[J].中国造纸学报,2022,37(2):71-80. [百度学术]
YUAN Q L, LI C X, XU L,et al. Analysis of Flow Field Characteristics of Negative Pressure Box During Air Laid Papermaking Based on Fluent[J].Transactions of China Pulp and Paper,2022,37(2):71-80. [百度学术]
李青华,李冬梅,刘德平,等.动力锂电池悬浮烘箱风速场特性分析与结构优化[J].机械设计,2021,38(8):31-37. [百度学术]
LI Q H, LI D M, LIU D P,et al. Analysis on the wind-speed field characteristics and the structure optimization of the power lithium battery’s suspension oven[J].Journal of Machine Design, 2021,38(8):31-37. [百度学术]
陈清华,吴佳乐,李东生,等.强制对流烘箱内温度场均匀性研究[J].科学技术与工程,2023,23(22):9509-9516. [百度学术]
CHEN Q H, WU J L, LI D S, et al. Uniformity of temperature field in forced convection oven[J]. Science Technology and Engineering, 2023,23(22):9509-9516. [百度学术]
JOSHI J, SAHU S K. Effect of single and multiple protrusions on thermal performance of slot jet impingement with curved surface[J].Applied Thermal Engineering,DOI:10.1016/j.applthermaleng, 2023,120757. [百度学术]
MARTÍNEZ-FILGUEIRA P, PORTAL-PORRAS K, FERNANDEZ-GAMIZ U, et al. Experimental and numerical modeling of an air jet impingement system[J].European Journal of Mechanics-B/Fluids,2022, 94:228-245. [百度学术]
李徐佳,高殿荣,王华山.锂电池极片干燥箱风刀内流特性的试验与数值模拟对比研究[J].机械工程,2015,51(24):105-111. [百度学术]
LI X J, GAO D R, WANG H S. Comparative study on experiment and simulation of the flow characteristics of air nozzles used in lithium battery film drying device[J].Journal of Mechanical Engineering,2015,51(24):105-111. [百度学术]
ZHENG X, GAO Y F. Analysis and structure optimization of the wind distribution of Nozzle in the gravure printing drying system[J].Applied Mechanics and Materials,2015,731:411-415. [百度学术]
翟银花.凹印机烘箱的风嘴设计及结构优化[D].西安:西安理工大学,2017. [百度学术]
ZHAI Y H. Design of nozzle and structure optimization of the gravure printer drying oven[D]. Xi’an:Xi’an University of Technology,2017. [百度学术]
刘腾.高精密涂布悬浮式烘箱的基材干燥特性研究与风嘴结构优化[D].西安:西安理工大学,2023. [百度学术]
LIU T. Research on the drying characteristics of substrate and optimization of air nozzle structure for high precision coating suspension ovens[D]. Xi’an:Xi’an University of Technology,2023. [百度学术]
程千驹,贺四清,胡泓,等.锂电池涂布烘箱风嘴射流压强分布优化研究[J].包装工程,2019,40(5):180-186. [百度学术]
CHENG Q J, HE S Q, HU H, et al. Jet pressure distribution optimization in air nozzle of lithium battery coating oven[J]. Packaging Engineering, 2019,40(5):180-186. [百度学术]
黄卿.包装印刷设备的烘干风嘴分布参数规律研究[J].包装工程,2020,41(11):219-226. [百度学术]
HUANG Q. Rule for the distribution parameters of air nozzles in packaging printing equipment[J]. Packaging Engineering,2020,41(11):219-226. [百度学术]
HUANG T, TAN P, ZHANG Y,et al.Heat transfer uniformity analysis of floatation nozzle using a revised uniformity indicator[J].International Journal of Heat and Mass Transfer, DOI:10.1016/j.ijheatmasstransfer.2020.120885. [百度学术]
AMINZADEH M, KHADEM J, ZOLFAGHARI S A,et al.Numerical study of nozzle width effect on cooling performance of a turbulent impinging oscillating jet in a heated cavity[J].International Communications in Heat and Mass Transfer: A Rapid Communications Journal, DOI:10.1016/j.icheatmasstransfer.2020.104899. [百度学术]
黄烨锋.宽幅多喷嘴风道数值模拟及流场均匀性优化[D].杭州:浙江理工大学,2021. [百度学术]
HUANG Y F. Numerical simulation and flow field uniformity optimization of wide multi nozzle duct[D].Hangzhou:Zhejiang Sci-Tech University,2021. [百度学术]
ERGUR E, CALISIR T.Numerical investigation of thermal and flow characteristics of impinging synthetic jet with different nozzle geometries at low nozzle-to-plate distances[J].International Journal of Thermal Sciences,DOI:10.1016/j.ijthermalsci.2023.108463. [百度学术]
PADHI A K, TAFIQ M, PATRA S, et al. Approval of estimating productivity of a versatile plasma bend cutting framework utilizing response surface methodology and desirability function[J].Materials Today Communications, DOI:10.1016/j.mtcomm.2023.107196. CPP [百度学术]