摘要
介绍了国内外对于磨浆机磨盘间隙测量的研究现状,以及磨浆机磨盘间隙在线测量的改进方法,进一步探讨了电涡流传感器在磨浆机上齿盘边界特性、齿盘变转速响应特性、进退盘响应特性、齿盘的静动态响应性能、输出特性等最佳特性曲线拟合方程。优化了电涡流传感器结合超声波测厚仪对磨浆机磨盘间隙的实时在线测量方案。传感器安装与磨片边缘的距离大于2 mm、动盘外缘线速度大于360 m/min时,电压值稳定,进退盘响应及静动态输出特性变化总体趋于一致,最佳特性拟合曲线方程线性系数大于0.99。
磨浆机是在高温高压条件下将木片及其他植物材料分离成植物纤维的重要设
磨浆机的动、定磨片处于动态磨损状态,故从外部测量磨损位移间隙存在较大困难;用非接触测量的方法在其内部测量,需耐受一定温度和磨浆介质。电涡流传感器不受磨浆介质和高温的影响,可以实现非接触式测量,具有灵敏度高、抗干扰能力强、能适应恶劣环境等特点,因此可以安装在定盘上,将动盘作为被测面来测量磨盘间隙。
磨浆机运行前需设置好磨盘工作初始间隙,但由于正常工作时磨片一直处于研磨过程中,磨片表面遭到多种不同形式磨损,从而导致磨盘间隙一直在动态变
电涡流传感器根据电磁场的原理工作。当被测金属置于变化的磁场中时,会产生闭合的涡流。涡流会产生电磁场来阻碍原有磁场的变化,导致线圈阻抗(Z)发生变化。Z的变化与金属导体的几何形状、电导率、磁导率、电流角频率及线圈与被测金属导体之间的距离密切相关。对于平面金属导体,Z可用
(1) |
其中,为磁导率;为电导率;为线圈半径;为线圈与被测金属导体之间的距离;为被测金属板厚度;为线圈电流;为电流角频率。当、、、、、保持不变时,Z可视为的单值函数。这样就构成了电涡流传感器,其中包括1个载流线圈和金属导体。金属导体在变化的磁场中形成涡流,存在集肤效应,被测导体不同厚度的电流密度与传感器线圈的激励电压和频率相关。
电涡流传感器工作原理图如
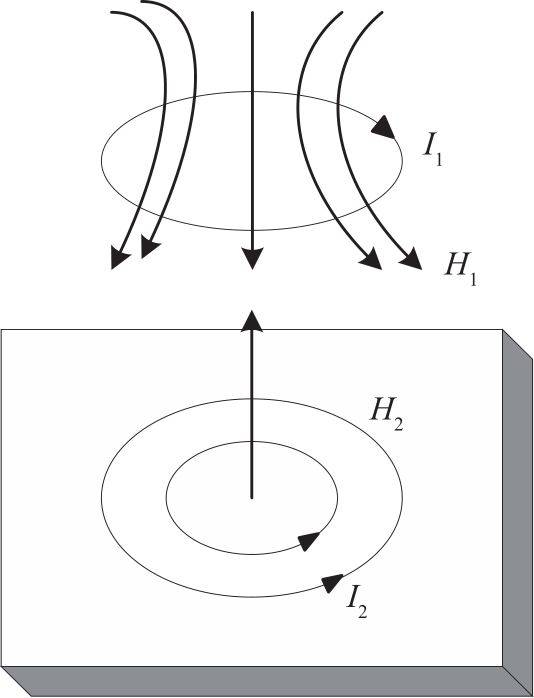
图1 电涡流传感器工作原理图
Fig. 1 Working principle diagram of eddy current sensor

图2 电涡流传感器等效电路模型
Fig. 2 Equivalent circuit model of eddy current sensor
根据基尔霍夫电压平衡方程,可列方程组如
(2) |
式中,R1为感应线圈电阻;U1为感应线圈电压;L1为感应线圈电感;R2为被测金属电阻;L2为被测金属电感;为电流角频率;M为互感系数,与线圈和被测金属之间的间距x有关。
由此,可以推导出线圈的等效阻抗Z,如
(3) |
感应线圈的等效电阻Re和等效电感Le计算如
(4) |
由
电涡流传感器可以实现在静态和非静态条件下对被测金属的非接触测量,且其具有线性范围宽、分辨率高、灵敏度高、有较强的抗干扰能力和不受介质影响等优点。因此,满足测量磨浆机磨盘间隙的基本条件。
根据相关研究成
超声波测厚仪可根据超声波脉冲反射的原理测量厚度。探头发射的超声脉冲通过耦合剂在物体内传播到达材料界面时,部分超声脉冲被反射回来,探头接收被测物体界面反射回来的回波。通过精确测量超声波在物体中的传播时间来确定被测物体的厚
(5) |
式中,v为材料声速,t为超声波在试件中往返1次的传播时间。
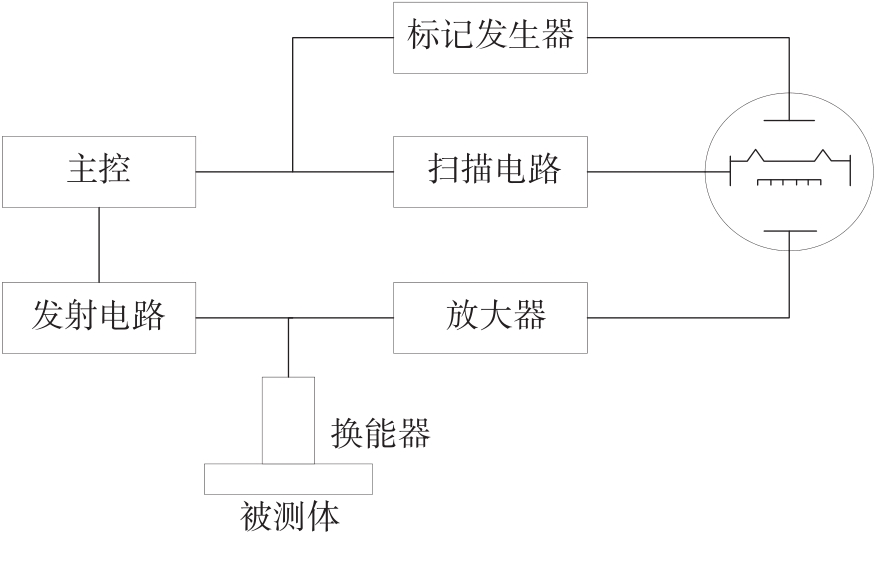
图3 超声波测厚原理图
Fig. 3 Schematic diagram of ultrasonic thickness measurement
电涡流传感器与齿盘边界安装示意图如
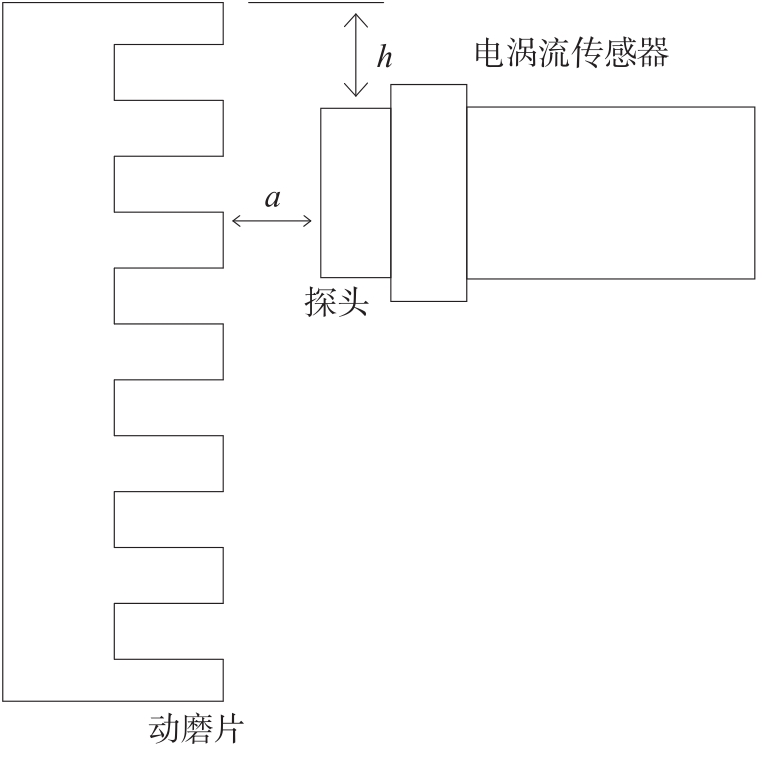
图4 电涡流传感器与齿盘边界安装示意图
Fig. 4 Installation diagram of eddy current sensor and tooth disk boundary
将电涡流传感器与齿盘试件安装于数控车床上,调整齿盘转速并保持在磨浆机正常工作时的线速度范围内。在齿盘与电涡流传感器探头处于不同距离的情况下,控制车床使电涡流传感器平行于齿盘试件表面移动,测量并记录电涡流传感器探头在不同位置时的输出特性。
确定电涡流传感器在磨盘边界的最佳安装距离后,在齿盘试件定磨盘周边安装2个处于相同圆周上的探头(以磨盘中心为圆心,相隔120°),在齿盘和电涡流传感器探头不同距离的情况下分静态(动盘不转)和动态(动盘空转),分别测量电涡流传感器的输出特性。
根据实验数据得出在电涡流传感器探头端面与盘面不同距离a下,控制车床,使电涡流传感器探头径向外边缘平行于齿面试件表面径向周边缘,径向距离h和电涡流传感器输出电压U之间的关系如
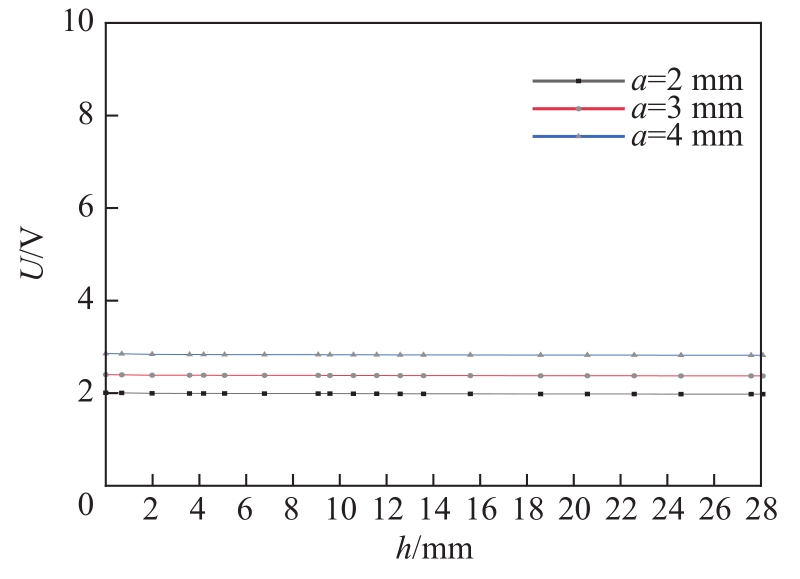
图5 径向距离与输出电压关系
Fig. 5 Relationship of radial distance and output voltage
从
由此可以得出,电涡流传感器的输出电压与其探头在磨盘周边的安装距离与齿形无关;与电涡流传感器探头端面与盘面距离a无关;电涡流传感器探头径向外端面与磨盘径向周边缘安装距离h应大于2 mm,但不能超出磨盘研磨区,否则不能准确反映出磨浆机研磨区之间的磨盘间隙。
通常磨浆机正常工作时,周边研磨区的线速度为1200~3000 m/min。本课题探究齿盘试件在不同转速和不同间隙下电涡流传感器输出电压的变化。结果表明,当齿盘试件外缘线速度小于360 m/min时,电涡流传感器的输出电压值在±0.02 V内波动;当齿盘试件外缘线速度大于360 m/min时,电涡流传感器的输出电压显示稳定,且外缘线速度越高,输出电压越稳定。这表明电涡流传感器完全可用于磨浆机磨盘间隙的在线测量。
模拟研究表明,电涡流传感器探头轴向端面与齿面之间的距离大于0.8 mm时进入线性范
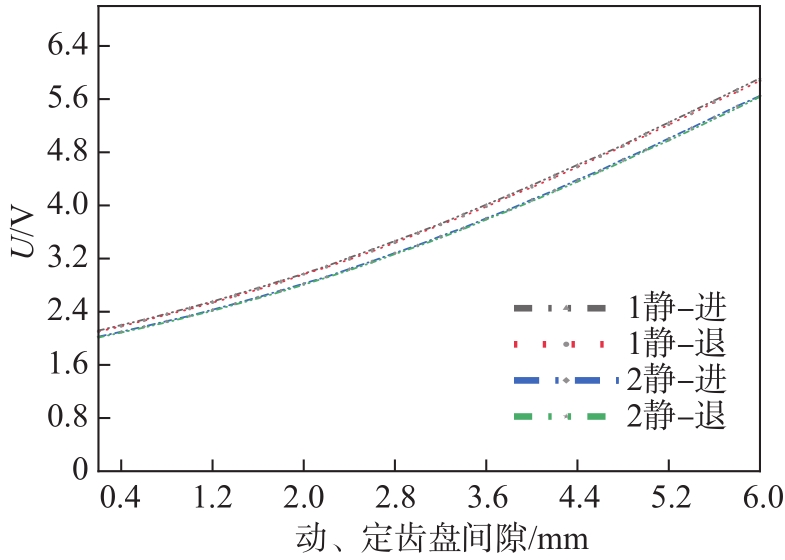
图6 静态下电涡流传感器的输出特性
Fig. 6 Output characteristics of eddy current sensor under static conditions
从
在动盘空转的情况下,电涡流传感器的输出特性如
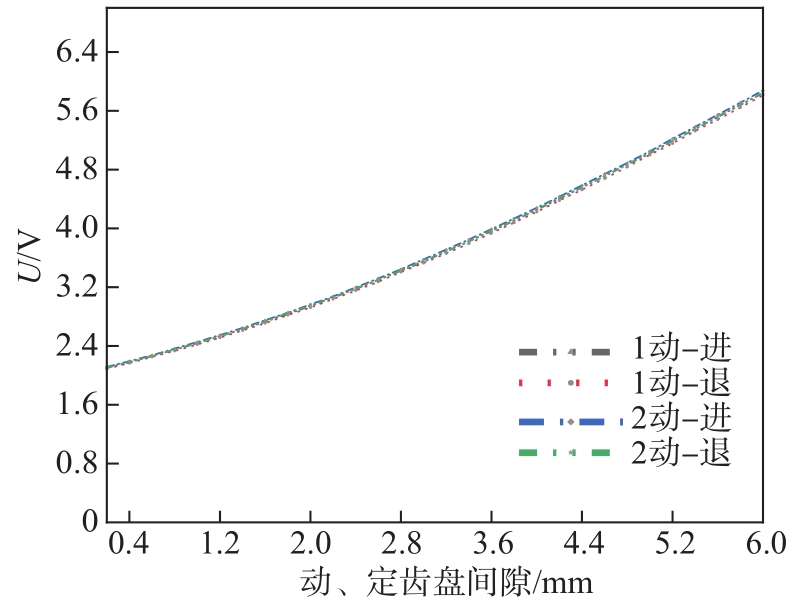
图7 动态下电涡流传感器的输出特性
Fig. 7 Output characteristics of eddy current sensor under dynamic conditions
在静、动态下,电涡流传感器的输出特性如
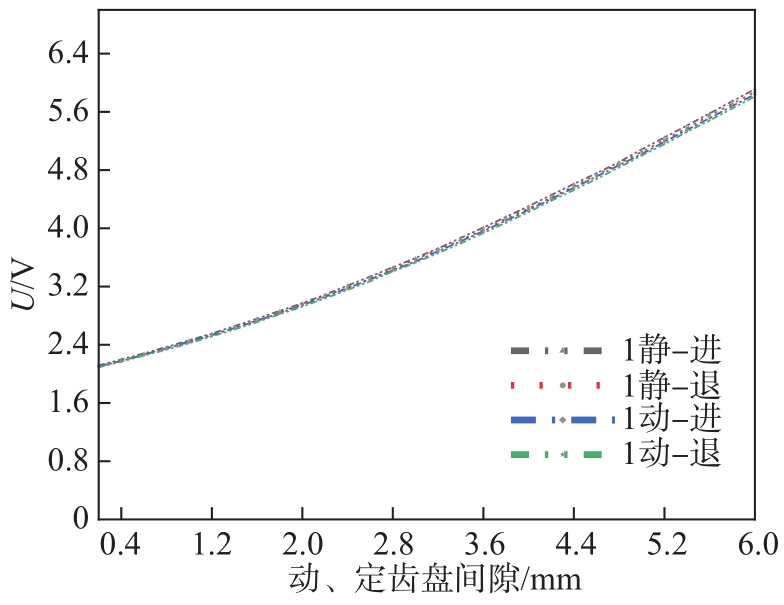
图8 静、动态下电涡流传感器1的输出特性
Fig. 8 Output characteristics of eddy current sensor 1 under static and dynamic conditions
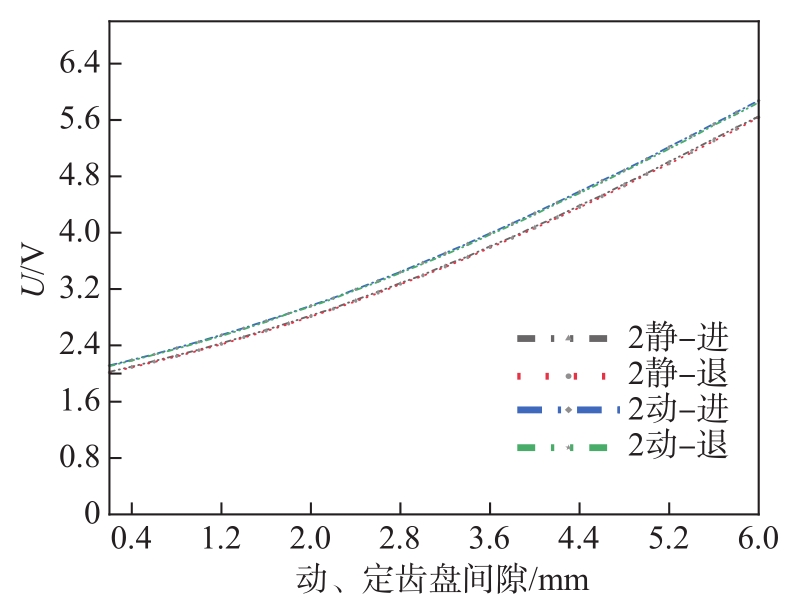
图9 静、动态下电涡流传感器2的输出特性
Fig. 9 Output characteristics of eddy current sensor 2 under static and dynamic conditions
电导率和磁导率是被测介质影响电涡流传感器的主要因素,电导率与磁导率越高时,涡流效应越明显,对电涡流传感器的输出特性影响越大。磨浆机工作时,磨盘之间的介质为各种不同浓度的浆料纤维。
将樟子松、水曲柳、毛竹等不同材种的浆料放置到电涡流传感器探头与被测金属板之间,稳定一段时间后测量电涡流传感器的输出电压。研究发现,几种浆料在绝干的条件下,对电涡流传感器的输出电压无任何影响;在含水率20%~100%的情况下,均能引起输出电压的微小下降,且含水率越高,输出电压下降越大,但总体变化极其微小,可忽略不计。
相关研究表
综上所述,不同材种且不同浓度的浆料对电涡流传感器输出电压基本无影响。
根据电涡流传感器的实验参数,采用最小二乘法进行线性回归,得最佳特性曲线拟合方程如
(6) |
式中,U为电涡流传感器输出电压,x为定磨盘与动磨盘之间的磨盘间隙。相关系数
本课题基于电涡流传感器和超声波测厚仪结合的方法对磨浆机磨盘间隙的在线测量进行了进一步探讨。因为磨浆机正常工作时,动、静磨盘齿面被不断磨损,造成齿面不断变矮。为保护电涡流传感器的探头不会随着齿面被磨损,在安装传感器时,将2个电涡流传感器探头端面在定磨盘齿面的基础上向内缩进2 mm。因磨浆机研磨区在高温、高压环境中工作,需在其探头表面添加非金属、硬度高、耐高温的保护性材料。将超声波测厚仪安装于定磨片的背面,测量其工作过程中的实时厚度变化。将2个电涡流传感器与超声波测厚仪安装在定磨盘边缘位置且处于相同圆周上,呈等边三角形排列,如
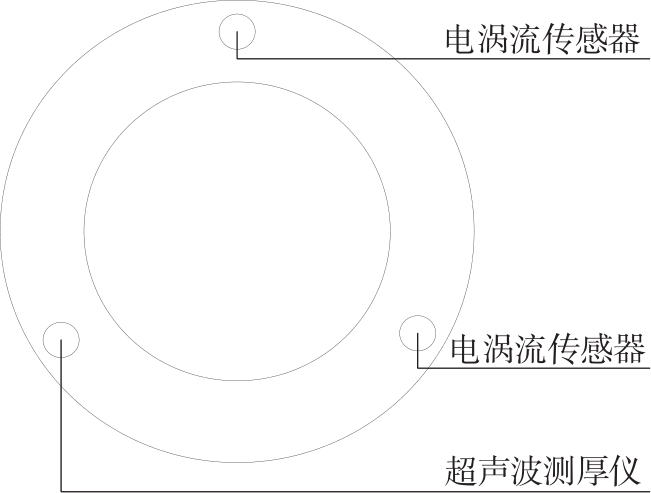
图10 电涡流传感器和超声波测厚仪安装示意图
Fig. 10 Installation diagram of eddy current sensor and ultrasonic thickness gauge
因为磨浆机的动磨片和定磨片的齿面结构、材料和安装位置等均一致和对称,假设磨浆机正常磨浆过程中,2个磨片基本处于相同磨损状态下,故磨片磨损造成磨浆机磨盘间隙的增加应为磨盘磨损量的2倍。在人为调整好初始磨盘间隙后,当因外部需求需要执行进、退盘操作时,磨盘间隙的变化量应为电涡流传感器探头端面到动磨盘齿面距离变化量的1倍。所以,磨浆机磨盘间隙计算如
(7) |
(8) |
式中,x1为磨浆机正常磨浆时的磨盘动态间隙,mm;x2为磨浆机进、退盘时的磨盘动态间隙,mm;a0为磨浆机磨盘的初始间隙,mm;U为2个电涡流传感器输出电压的均值,V;U01、U02为电涡流传感器1和2在磨浆机运行前初始间隙时的输出电压,V;b为传感器的灵敏度,V/mm。
以固定磨浆机定磨片的背面作为测量基准,如
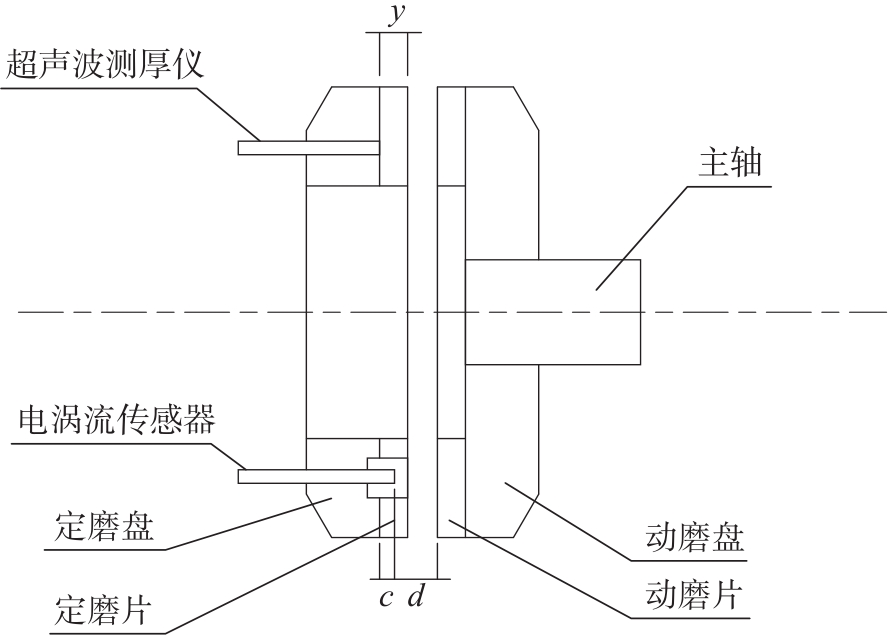
图11 超声波测厚仪测量磨盘间隙的原理
Fig. 11 Principle of ultrasonic thickness gauge to measure the disc clearance
(9) |
式中,e为动、定磨片齿面之间的距离,mm;d为2个电涡流传感器探头到动磨片齿面距离之和,mm;c为2个电涡流传感器探头端面到定磨片背面距离之和,mm;y为超声波测厚仪测量定磨片磨损后的厚度,mm。
综上所述,磨浆机正常磨浆时的磨盘间隙值(x3)计算如
(10) |
进、退盘时磨浆机磨盘间隙值(x4)计算如
(11) |
4.1 电涡流传感器应尽量安装在靠近磨浆机齿盘边缘,但需要考虑磨盘周边输出特性变化的影响。电涡流传感器探头在磨盘周边的安装距离与齿形无关,与电涡流传感器探头端面与盘面距离无关;电涡流传感器探头径向外端面与磨盘径向周边缘距离应大于2 mm,但不能超出磨盘研磨区。
4.2 当齿盘试件外缘线速度小于360 m/min时,电涡流传感器的电压值在±0.02 V内波动;当齿盘试件外缘线速度大于360 m/min时,电涡流传感器的电压显示稳定,且转速越高,电压越稳定。
4.3 电涡流传感器测量磨盘间隙时静、动态输出特性变化总体趋于一致;进、退盘操作对电涡流传感器输出结果基本无影响;在实际磨浆机磨盘间隙正常工作范围内线性度较好。
4.4 电涡流传感器测量磨盘间隙时不受浆料类别和浓度的影响。
参 考 文 献
刘庆立, 汤 伟, 王孟效. 盘磨机磨盘磨损检测技术的研究[J]. 中国造纸, 2017, 36(1): 47-51. [百度学术]
LIU Q L, TANG W, WANG M X. Research on Detection Technology of Grinding Disc Wear in Disk Mill[J]. China Pulp & Paper, 2017, 36(1): 47-51. [百度学术]
邢宇航, 董继先, 刘彦龙, 等. 盘磨机磨盘间隙实时在线检测技术研究进展[J]. 中国造纸, 2020, 39(12): 75-80. [百度学术]
XING Y H, DONG J X, LIU Y L, et al. Research Progress on Real-time On-line Detection Technology of Disc Clearance in Disc Mill[J]. China Pulp & Paper, 2020, 39(12): 75-80. [百度学术]
王宝金. 热磨机磨盘实际间隙精确测量与主轴运行状态监测的研究[D]. 南京: 南京林业大学, 2004. [百度学术]
WANG B J. Research on Accurate Measurement of Actual Clearance of Hot Mill Disc and Monitoring of Spindle Running State[D]. Nanjing: Nanjing Forestry University, 2004. [百度学术]
NORDMAN L, LEVLIN J E, MARKONEN T, et al. Conditions in an LC-refiner as observed by physical measurements[J]. Paperi ja Puu-Papper, 1981, 63(4): 169-180. [百度学术]
MAY W D. System for displaying out-of-tram measurements in disc refiners: US3500179[P]. 1970-03-10. [百度学术]
KÄRNÄ J, PAHLMAN H. Method and device for measuring the distance between the discs of a refiner using a measurement of the magnetic flux induced between the discs: WO88/003054P1[P]. 1989-10-31. [百度学术]
张 辉. 造纸盘式磨浆机磨浆间隙在线、精确测量技术原理与方法[D]. 南京: 南京林业大学, 2008. [百度学术]
ZHANG H. Principle and Method of On-line and Accurate Measurement of Pulp Clearance of Paper Disc Pulping Machine[D]. Nanjing: Nanjing Forestry University, 2008. [百度学术]
姚 俊, 王 平. 盘磨机磨盘间隙的测量与调节方法[J]. 中国造纸, 2012, 31(1): 67-71. [百度学术]
YAO J, WANG P. Measurement and Adjustment Method of Disc Clearance in Disc Mill[J]. China Pulp & Paper, 2012, 31(1): 67-71. [百度学术]
王佳辉, 王 平. 盘磨机的研究现状与发展趋势[J]. 中国造纸, 2014, 33(9): 51-55. [百度学术]
WANG J H, WANG P. Research Status and Development Trend of Disc Mill[J]. China Pulp & Paper, 2014, 33(9): 51-55. [百度学术]
张 辉, 李忠正, 范 文. 电涡流传感器测量旋转齿盘位移的特性研究[J]. 振动、测试与诊断, 2008(1): 44-49, 77-78. [百度学术]
ZHANG H, LI Z Z, FAN W. Study on Characteristics of Eddy Current Sensor for Measuring Displacement of Rotating Tooth Disc[J]. Journal of Vibration, Measurement & Diagnosis, 2008(1): 44-49, 77-78. [百度学术]